-
Precision Sheet Metal Fabrication
-
Stainless Steel Sheet Metal Fabrication
-
Sheet Metal Stamping
-
Automotive Sheet Metal Components
-
Medical Equipment Parts
-
Sheet Metal Assembly
-
Plastic Injection Molding
-
Sheet Metal Forming
-
Sheet Metal Welding
-
Metal Laser Cutting
-
Sheet Metal Bending
-
Sheet Metal Powder Coating
-
Custom Metal Fabrication
-
Custom Plastic Molding
-
Customized Metal Bracket
-
Custom Metal Enclosures
-
Windmill Parts
New Energy Vehicles Car Busbar OEM Tooling Die Stamping
Place of Origin | Nantong,CHINA |
---|---|
Brand Name | Strong,OEM or ODM |
Certification | SO9001, IATF-16949, ISO-3834, ISO-14001, etc |
Model Number | Auto-003 |
Minimum Order Quantity | 100,00PCS |
Price | USD 2~50/PCS |
Packaging Details | Pearl cotton, foam, wrapping tape, carton, cardboard, pallet, etc. |
Delivery Time | 30 working days |
Payment Terms | L/C, D/A, D/P, T/T, Western Union, MoneyGram |
Supply Ability | 3*40HQ/month |
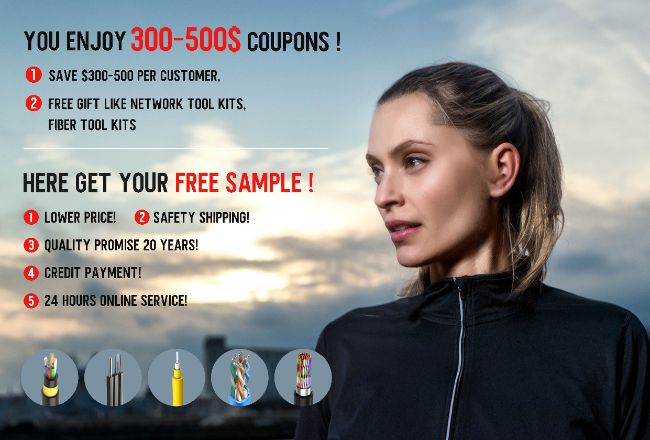
Contact me for free samples and coupons.
Whatsapp:0086 18588475571
Wechat: 0086 18588475571
Skype: sales10@aixton.com
If you have any concern, we provide 24-hour online help.
xName | New Energy Vehicles Busbar | Material | Aluminum Alloy Or Copper Busbar |
---|---|---|---|
Certificate | SO9001, IATF-16949, ISO-3834, ISO-14001, Etc | Shape | Rectangular Busbars/Round Busbars/Tubular Busbars/Flexible Busbars/Insulated Busbars/High Voltage Busbars/Custom Busbars |
Application | Switchboards(panelboards), ,motor Control Centers,distribution Centres,transformers,electric Motors,generators Etc. | Other | Need Customer Provide Current Rating,voltage Rating,Length,Cross-sectional Area,thickness,ambient Temperature |
Highlight | New Energy Vehicles Car Busbar,OEM Car Busbar,OEM tooling die stamping |
1. New Energy Vehicles Busbar
Our New Energy Vehicles Busbar is a high-quality metal part designed for the power transmission and distribution systems in new energy vehicles. It is an essential component for the efficient and reliable operation of electric and hybrid vehicles.
Our Busbars are made using premium materials such as copper or other materials as per customer's requirements, ensuring exceptional conductivity and durability. We use a precision manufacturing process that includes CNC machining, bending, forming, and welding to ensure that our busbars meet the highest standards of accuracy, quality, and performance.
In the current market, the demand for high-quality New Energy Vehicles Busbars is increasing, driven by the growing popularity of electric and hybrid vehicles. Our busbars are an ideal choice for automotive manufacturers and enthusiasts seeking to improve the power transmission and distribution systems of their vehicles.
At our company, we can provide customers with OEM or even ODM services, ensuring that our New Energy Vehicles Busbars meet their specific requirements and design specifications. Our team of experienced engineers and technicians is dedicated to providing the highest level of customer service and support, from design and prototyping to production and delivery.
Overall, our New Energy Vehicles Busbars represent an ideal solution for automotive manufacturers and enthusiasts seeking high-quality metal parts that offer exceptional conductivity, durability, and performance. With our customizable options and OEM/ODM services, we are committed to delivering the highest level of quality and satisfaction to our customers.
2. Product parameters
New Energy Vehicles Busbar | |||
Size | Customized to fit specific vehicle models and design requirements | ||
Color | Silver,Orange, custom | ||
Material | Copper or other materials as per customer's requirements | ||
Process | CNC machining, bending, forming, welding | ||
Tolerance | ±0.1mm or as per customer's requirements | ||
Surface Treatment | Tin plating, silver plating, or as per customer's requirements | ||
Application | New energy vehicles, power transmission and distribution systems | ||
Thickness | Customized to fit specific vehicle models and design requirements | ||
Shape | Customized to fit specific vehicle models and design requirements | ||
Mold making time | 25 working days | ||
Delivery date | About 30-35 working days | ||
Certification | ISO 9001:2015, RoHS, or as per customer's requirements | ||
Price | Need to negotiate between buyer and seller | ||
Packaging Details | Box/foam/pearl cotton/carton/tray/customized | ||
Supply Ability | 30000+ PCS/Month | ||
Payment Terms | L/C, D/A, D/P, T/T, Western Union, MoneyGram |
3. Materials used
Busbars are commonly made of copper or aluminum, as these materials have excellent electrical conductivity and are readily available. Copper is the preferred material for high-current applications because it has a higher conductivity than aluminum. However, aluminum is a more cost-effective option for low to medium current applications, and it is also lighter than copper, making it easier to handle and install. Other materials such as brass, bronze, and steel can also be used for busbars, but they are less common. The material used for a busbar depends on factors such as the current rating, the environment in which it will be used, and the cost.
4. Shape
Busbars come in a variety of shapes and sizes depending on their intended use. The most common shapes for busbars are rectangular, round, and tubular. Rectangular busbars are flat strips of metal with a rectangular cross-section, and they are the most commonly used shape for power distribution. Round busbars are cylindrical in shape and are often used in applications where space is limited. Tubular busbars have a hollow, cylindrical shape and are commonly used in high-power applications where cooling is required, as they allow for the circulation of coolant through the center of the tube.
In addition to these basic shapes, busbars can be formed into a variety of complex shapes to fit specific applications. For example, busbars can be bent, twisted, or shaped into curves to fit around obstacles or to make connections at non-standard angles. The shape of a busbar depends on the specific requirements of the application, such as the current rating, voltage, and space constraints.
5. Dimensioning
The dimensioning of a busbar involves determining the appropriate size and shape of the busbar to ensure that it can safely carry the required electrical current without overheating or sustaining damage. The key factors to consider when dimensioning a busbar include the current rating, the voltage, the ambient temperature, and the material properties.
The cross-sectional area of the busbar is directly proportional to its current carrying capacity. A larger cross-sectional area means that the busbar can carry more current without overheating. The thickness of the busbar is also important, as it affects the resistance of the busbar. A thicker busbar will have a lower resistance and therefore generate less heat than a thinner busbar.
The voltage rating of the busbar is also important, as it determines the insulation requirements and the distance between busbars. Higher voltages require greater insulation and larger distances between busbars to prevent arcing.
The ambient temperature is another important factor, as it affects the temperature of the busbar and the surrounding air. Higher ambient temperatures can reduce the current carrying capacity of the busbar, and therefore a derating factor may need to be applied to the busbar's current rating.
Finally, the material properties of the busbar, such as its thermal conductivity and coefficient of thermal expansion, can affect its performance. For example, copper has a higher thermal conductivity than aluminum, which means that a copper busbar will dissipate heat more effectively.
In summary, the dimensioning of a busbar involves selecting theappropriate cross-sectional area, thickness, voltage rating, and insulation based on the current rating, voltage, ambient temperature, and material properties. This ensures that the busbar can safely carry the required current without overheating or sustaining damage.
6. Busbar Insulation
Busbar insulation is an important consideration in electrical systems to prevent accidental contact and electrical arcing. Insulation is used to cover the busbar and prevent it from coming into contact with other conductive materials or surfaces. The type of insulation used depends on the specific requirements of the application, such as the voltage rating, the ambient temperature, and the space constraints.
Some common types of busbar insulation include:
(1). Heat-shrink tubing: This is a type of plastic tubing that can be shrunk over the busbar using heat. It provides a simple and cost-effective way to insulate busbars.
(2). PVC or fiberglass sleeves: These are pre-manufactured sleeves that can be slid over the busbar. They provide good insulation and are available in a variety of sizes and shapes.
(3). Epoxy powder coating: This is a type of coating that is applied to the surface of the busbar to provide insulation. It provides excellent resistance to moisture and chemicals, and can be applied in a variety of thicknesses.
(4). Insulating tape: This is a type of adhesive tape that can be wrapped around the busbar to provide insulation. It is a cost-effective way to insulate busbars, but may not provide as much protection as other insulation methods.
The insulation used for a busbar depends on the specific requirements of the application. Factors such as the voltage rating, the ambient temperature, and the space constraints should be considered when selecting the appropriate insulation method.
7. Fixed busbar
A fixed busbar is a type of electrical conductor that is permanently installed in a power distribution system. It is typically made of copper or aluminum and is used to distribute electrical power from a power source to multiple loads or devices. Fixed busbars are called "fixed" because they are not intended to be easily removable or reconfigurable.
Fixed busbars are commonly used in industrial and commercial power distribution systems, as well as in large-scale renewable energy installations. They are typically housed in an enclosure made of insulating materials to prevent accidental contact and electrical arcing. The enclosure also provides protection against environmental factors such as dust, moisture, and temperature fluctuations.
Fixed busbars can be designed in a variety of shapes and sizes depending on the specific requirements of the application. They can be rectangular, round, or tubular in shape, and can be formed into complex shapes to fit around obstacles or to make connections at non-standard angles. The cross-sectional area and thickness of the busbar are important factors to consider when designing a fixed busbar, as they affect the current carrying capacity and resistance of the busbar.
In summary, fixed busbars are an essential component of power distribution systems and are used to safely and efficiently distribute electrical power to multiple loads or devices. They are permanent installations and are designed to withstand the environmental conditions and electrical loads of the application.
8. Study of the differences between fixed and flexible busbars
Fixed and flexible busbars are two types of electrical conductors that are used in power distribution systems. While they both serve the same purpose of distributing electrical power to multiple loads, there are some key differences between them:
(1). Flexibility: The most obvious difference between fixed and flexible busbars is their flexibility. Fixed busbars are designed to be rigid and are not intended to be easily bendable or reconfigurable. Flexible busbars, on the other hand, are designed to be flexible and bendable, making them ideal for applications where vibration or movement is expected, or where space is limited.
(2). Installation: Fixed busbars are typically installed permanently in a power distribution system, while flexible busbars can be easily repositioned or replaced as needed.
(3). Current carrying capacity: Fixed busbars are typically designed to carry higher current loads than flexible busbars. This is because fixed busbars are made of a larger cross-sectional area of copper or aluminum, and are typically thicker than flexible busbars. Flexible busbars are designed to carry lower current loads, and are made of multiple layers of thin copper or aluminum strips laminated together with an insulating material.
(4). Cost: Flexible busbars are generally more expensive than fixed busbars due to their more complex design and the use of multiple layers of materials.
In summary, the main differences between fixed and flexible busbars are their flexibility, current carrying capacity, installation method, and cost. Fixed busbars are rigid and permanently installed, whileflexible busbars are designed to be bendable and reconfigurable. Fixed busbars are typically designed to carry higher current loads and are less expensive than flexible busbars. Flexible busbars, on the other hand, are designed to carry lower current loads and are more expensive due to their complex design. The choice between fixed and flexible busbars depends on the specific requirements of the application, such as the current rating, space constraints, and potential for movement or vibration.
9. Our advantage:
1) Five production branches
A total of 5 factories in China and Vietnam maintain a stable supply chain for customers;
2) Sign a non-disclosure agreement
We keep your ideas and designs completely confidential;
3) Comprehensive production line
Sheet metal stamping and injection molded parts are comprehensive. We have our own assembly line, paint line, one-stop service;
4) Experienced business development team
We have 15 business development experts with good English ability and communication skills to keep abreast of your needs;
5) We have a professional engineering team
Half of them have more than 15 years of experience in the mold industry, especially in molds, forming products, sheet metal products, stamping products and injection molding products;
6) We are an innovative company
We actively develop the Internet, medical equipment, aerospace, new energy storage, automobile and other industries, and develop the latest technology to meet the high production requirements of customers;
7) Fast delivery time
We have advanced technical processing machines and time-mobilized personnel, so we can complete prototype projects within 3-5 days, prototype molds within 15 days, and mass-produce complex molds within 3-5 weeks;
8) Quality control experts
We have passed ISO9001 quality management system certification, and can even apply for certificates for various quality products according to customer needs. On-site material, tool and part inspection before production and delivery.
10.Our factory
Shanghai Strong Metal Production was established in June 2003 with a total registered capital of 67 million yuan and a total construction area of 30,000 square meters. There are 5 factories in total, located in Nantong, Taicang, Nanjing, Vietnam and Shanghai.
The main products of our factory are OEM and ODM metal and plastic manufacturing services. Focusing on metal manufacturing, it has comprehensive capabilities such as independent mold design, metal stamping, sheet metal, laser cutting, powder coating, welding, and injection molding.
The company has more than 500 employees and more than 40 engineers, including engineering engineers, drafting engineers, quality engineers, process engineers, etc. engineer. We can provide services from drawings to samples and batches, and 24-hour technical support.
We have many advanced production equipment: more than 50 punching machines (up to 1000 tons), more than 20 injection molding machines (up to 740 tons), more than 20 bending machines (up to 600 tons), more than 20 automatic welding arms, more than 50 Welding table, 8+ laser cutting machine, 400m powder spraying line, etc. In terms of QC testing tools, we have CMM, two-dimensional measuring instrument, hardness tester, etc. (contact us if you need it, and we will provide you with a list of related equipment )
In 2021, Shanghai Strong Metal Production's annual turnover has exceeded 200 million yuan. We will continue to find and provide customers with better solutions, create more value, and create a better world.
11.Our production line
12. FAQ
Q: How long is your delivery time?
A: Generally it is 5-10 days if the goods are in stock. or it is 15-20 days if the goods are not in stock,
it is according to quantity.
Q: What are your terms of payment?
A: Payment<=1000USD, 100% in advance. Payment>=1000USD, 30% T/T in advance ,balance
before shipment.
Q: Do you provide samples? is it free or extra?
A: Yes, we could offer the sample for free charge but do not pay the cost of freight.
Q: Are you a trading company or manufacturer?
A: We are a manufactory.
If you have another question, pls feel free to contact us.